|
Welchen Normen gelten für Tellerfedern?
Für Tellerfedern gibt es die Normen DIN 2092 (Tellerfedern, Berechnung) und DIN 2093 (Tellerfedern, Maße, Qualitätsanforderungen). Diese Normen enthalten weitgehende Qualitätsforderungen für Ausführung, Grenzabmaße, Werkstoff, zulässige Spannungen, zulässiges Nachsetzen, Führungsspiel und Prüfung von Tellerfedern. Die Normen bilden die Grundlage der SCHNORR-Fertigung auch für die nicht in der DIN aufgeführten Abmessungen.
Hinweis (Febr. 2017):
Die Tellerfeder-Normen (DIN 2092-Berechnung von Tellerfedern und DIN 2093-Qualitätsanforderungen, Maße) sind ab sofort zurückgezogen. Die Normen wurden ersetzt durch die europäisch gültigen Normen:
DIN EN 16983 – Qualitätsanforderungen, Maße DIN EN 16984 - Berechnung
Die Einteilung in Gruppen und Reihen, sowie Dimensionen, Toleranzen und Herstellungsverfahren sind gleich geblieben. Es ergeben sich soweit keine Änderungen.
nach oben
|
|
Weshalb werden Standard-Tellerfedern in Gruppen (1, 2 , 3) eingeteilt?
Abhängig von der Dicke der Feder werden Tellerfedern nach einem von drei Formgebungsverfahren gefertigt:
- Gruppe 1
t < 1,25 mm, Stanzen, Kaltformen, Kantenrunden
- Gruppe 2
1,25 ≤ t ≤ 6 mm, Stanzen, Kaltformen, Drehen und Kantenrunden oder Feinschneiden, Kaltformen und Kantenrunden
- Gruppe 3
ab 6 mm, Kalt- oder Warmformen, allseits drehen, Kantenrunden oder Stanzen, Kaltformen, Drehen und Kantenrunden oder Feinschneiden, Kaltformen, Kantenrunden
Weitere Details siehe hier bei Herstellung.
Für diese Gruppen gelten unterschiedliche Toleranzen (Geometrie, Kräfte).
nach oben
|
|
Welche Bedeutung haben die Buchstaben A, B und C bei Standard-Tellerfedern?
Die DIN EN 16983 enthält drei Maßreihen für Tellerfedern, die sich in den Verhältnissen Aussendurchmesser/Dicke und lichte Höhe/Dicke unterscheiden. Tellerfedern mit gleichem Aussen- und Innendurchmesser sowie unterschiedlicher Dicke werden durch die vorlaufenden Buchstaben A (steile Kennlinie, harte Tellerfeder), B (mittelhart...) und C (weich, flache Kennline) unterschieden. Eine praktische Bedeutung haben diese Buchstaben jedoch nicht.
Neben den in DIN EN 16983 enthaltenen Abmessungen fertigt SCHNORR eine Vielzahl weiterer Federgrößen nach eigener Werksnorm, für die ebenfalls die Gütevorschriften der DIN EN 16983 anwendet werden. Diese Tellerfedern, deren Abmessungen nicht in der DIN EN 16983 aufgeführt sind, sind nicht durch A, B oder C gekennzeichnet.
nach oben
|
|
Weshalb werden Tellerfedern der Gruppe 3 bzw. mit Dicke > 6 mm mit Auflageflächen gefertigt?
Diese Tellerfedern werden an den Stellen I und III mit kleinen Auflageflächen (ca. 1/150 des Aussendurchmessers) versehen, die den Punkt der Krafteinleitung besser definieren und insbesondere bei Federsäulen die Reibung an den Führungselementen vermindern. Die Folge ist eine Verkürzung des Hebelarms und eine Erhöhung der Federkraft. Diese wird wieder ausgeglichen durch die Reduzierung der Tellerdicke t auf t’ (bei gleicher Bauhöhe).
t' muß bei Parallelschichtung zur Ermittlung der Säulenlänge berücksichtigt werden.
nach oben
|
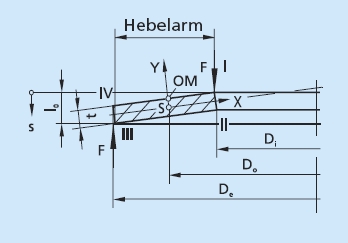
|
Worauf ist bei der Auswahl von Tellerfedern zu achten?
Eine falsche Auswahl kann leicht zu hohen Folgekosten, wie Imageverlust für das eigene Produkt oder Austauschkosten, führen. Im Vergleich dazu ist die Investition in eine hochwertige Tellerfeder geringer. Die folgenden Kriterien sind neben Kräften und Wegen wichtig:
- Welcher Einbauraum steht zur Verfügung?
- Wird die Tellerfeder(-anordnung) statisch oder dynamisch belastet?
- Für welche Anzahl von Lastwechseln ist die Tellerfeder(-anordnung) auszulegen (Zeitfestigkeit, Dauerfestigkeit)?
- Welchen Umgebungsbedingungen ist die Tellerfeder(-anordnung) ausgesetzt (Temperatur, Medium, Korrosion etc.)?
Als Hilfsmittel können Sie die Checkliste verwenden sowie unser Berechnungsprogramm, das Sie hier anfordern können. Gerne unterstützen wir Sie mit unserer Erfahrung und unserem Know-how.
nach oben
|
|
Wie werden Tellerfedern berechnet?
Die Berechnung der Federkräfte einer Tellerfeder stützt sich auf ein Modell von Almen und László. Ihre Genauigkeit im nutzbaren Bereich der Kennlinie ist sehr gut. Allerdings gibt es in der Praxis am Beginn der Einfederung eine Art Einschwingvorgang, der entsteht, weil Tellerfedern nie vollkommen symmetrisch sind. Sie werden zunächst quasi plangedrückt. Ebenso steigt die Federkraft im letzten Teil der Kennlinie in Wirklichkeit stärker an, wenn eine Feder zwischen zwei parallelen Flächen belastet wird, da sich aufgrund ihrer nie hundertprozentig ebenen Oberflächen Veränderungen des Hebelarmes ergeben.
Zur Berechnung stellen wir Ihnen gern ein Excel-Programm zur Verfügung, das Sie hier anfordern können
nach oben
|
|
Wann spricht man von statischer Belastung?
Ruhende oder selten wechselnde Beanspruchung liegt vor:
- bei Tellerfedern, die nur statisch ohne Laständerung belastet sind
- bei Tellerfedern mit gelegentlichen Last änderungen in größeren Zeitabständen und weniger als 10.000 Lastspielen während der vorgesehenen Lebensdauer.
Die Bauhöhe l0 einer Tellerfeder wird üblicherweise so ausgelegt, dass die Feder bei ruhender oder selten wechselnder Belastung flachgedrückt werden kann, ohne dass sich das Maß l0 über die zulässigen Abweichungen hinaus vermindert. Hierfür ist die Spannung σOM an der Stelle OM maßgebend.
Plastische Verformungen treten auf, wenn in bestimmten Bereichen die Streckgrenze des Werkstoffes überschritten wird. Zur Beurteilung wird als Vergleichsspannung die Spannung σOM herangezogen. Ihr Betrag bei Planlage sollte nicht größer sein als der Betrag der Zugfestigkeit Rm des jeweiligen Werkstoffes. Für Federstähle nach DIN 17221 und DIN 17222 gilt Rm≈1600N/mm2. Bei anderen Werkstoffen müssen die dafür gültigen Werte für die Zugfestigkeit berücksichtigt werden. Einige der in den Tabellen aufgeführten Federn überschreiten die zulässige Beanspruchung an der Stelle OM. Bei derartigen Federn besteht die Möglichkeit eines geringen Nachsetzens.
nach oben
|
|
Was ist bei dynamischer Belastung von Tellerfedern zu beachten?
Die meisten Tellerfedern können nur begrenzte dynamische Belastung ertragen. Hier sind sowohl die Lastspanne als auch das Lastniveau von Bedeutung. Die zu erwartende Lebensdauer einer Tellerfeder unter einer vorgegebenen Lastsituation kann anhand von Schaubildern abgeschätzt werden. Zudem ist es erforderlich, Tellerfedern auf mindestens 15% bis 20% ihres möglichen Federweges vorzuspannen, damit Zug-/Druck-Wechselspannungen in der Feder bei Beginn der Einfederung vermieden werden
Schwingende Beanspruchung liegt bei allen Tellerfedern vor, bei denen die Belastung dauernd zwischen einem Vorspannfederweg s1 und einem Federweg s2 wechselt. Unter dem Einfluss der Hubspannung σh können schwingend belastete Tellerfedern je nach Lebensdauer in zwei Gruppen eingeteilt werden: (siehe auch DIN 50100):
- Tellerfedern mit hoher Lebensdauer. Diese Tellerfedern sollen ohne Bruch mindestens 2 x 106 Lastwechsel und mehr ertragen.
- Tellerfedern mit begrenzter Lebensdauer. Diese Tellerfedern sollen im Bereich der Zeitfestigkeit
104 ≤ N < 2 x 106 eine begrenzte Anzahl von Lastspielen bis zum Bruch erreichen.
Für Tellerfedern mit schwingender Beanspruchung sind die rechnerischen Zugspannungen an der Federunterseite maßgebend, da Dauerbrüche stets von hier ausgehen. In Abhängigkeit von den Maßverhältnissen δ = De/Di und h0/t und der relativen Einfederung s/h0 kann die größte Hubspannung σh sowohl an der Stelle II als auch an der Stelle III auftreten.
nach oben
|
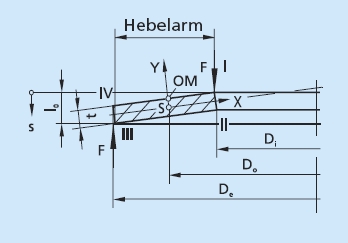
|
Weshalb müssen Tellerfedern bei dynamischer Belastung mit einer hinreichend hohen Vorspannung ausgelegt werden?
Nach der Vergütung werden alle Tellerfedern vorgesetzt, was eine plastische Verformung im Bereich der Querschnittsstelle I zur Folge hat. Dadurch entstehen in diesem Bereich Zugeigenspannungen an der unbelasteten Feder. Bei Belastung tritt dann ein Wechsel zwischen Zug- und Druckspannung ein, der bei dynamischer Beanspruchung zu Anrissen führt. Um diese zu vermeiden, müssen die Zugeigenspannungen durch entsprechende Vorspannung ausgeglichen werden. Schwingend belastete Tellerfedern sollten deshalb mindestens auf s = 0,15 bis 0,20 h0 vorgespannt werden.
nach oben
|
|
Welche Kombinationsmöglichkeiten gibt es für Tellerfedern?
Die Form der Tellerfeder als kegelförmige Ringschale erlaubt es, Einzelfedern auf verschiedene Weise zu kombinieren. Damit kann die Kennlinie einer Federanordnung fast beliebig variiert und den Erfordernissen angepasst werden. Prinzipiell gibt es folgende Möglichkeiten:
- Wechselsinnige Schichtung zu Federsäulen (Hintereinanderschaltung)
- Gleichsinnige Schichtung zu Federpaketen (Parallelschaltung)
- Wechselsinnige Schichtung von Federpaketen zu Federsäulen
Durch besondere Massnahmen (Kombination unterschiedlich dicker Tellerfedern, Verwendung von Zwischenscheiben etc.) kann man auch progressive Kennlinien erreichen. Wegen des damit verbundenen Aufwands haben derartige Lösungen keine grosse praktische Bedeutung.
nach oben
|
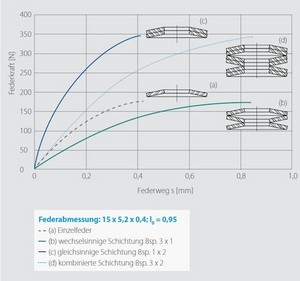
|
Was ist bei der Auslegung von Tellerfedersäulen zu beachten?
Tellerfedern werden häufig nicht als einzelne Feder, sondern paketiert (mehrere Federn gleichsinnig), als Säule (mehrere Federn wechselsinnig) oder in Kombination eingesetzt, siehe oben bei Kombinationsmöglichkeiten.
Die beste Federanordnung ist diejenige, die mit der kleinstmöglichen Zahl von Einzelfedern auskommt. Um dieses Ziel zu erreichen, sollte der Außendurchmesser stets so groß wie möglich gewählt werden. Dadurch wird automatisch die Säulenlänge kurz gehalten. Mit zunehmender Anzahl von Tellerfedern in der Säule vergrößert sich die Reibung und die ungleichmäßige Einfederung einzelner Teller in der Säule. Als Richtwert für die Säulenlänge empfehlen wir: L0 < 3 x De. Lässt sich eine größere Säulenlänge nicht vermeiden, dann sollte die Säule durch geeignete Scheiben, die möglichst exakt geführt werden, in zwei oder drei Teilsäulen unterteilt werden
Um die Reibung in vertretbaren Grenzen zu halten, sollten bei Mehrfachschichtung möglichst nicht mehr als 2 bis 3 Federn parallel geschichtet werden, es sei denn, ein großer Reibungsverlust ist ausdrücklich erwünscht. Insbesondere bei dynamischer Belastung ist schon bei 2-fach-Schichtung mit einer erheblichen Erwärmung zu rechnen.
Wenn möglich, sollten die Enden einer Tellerfedersäule mit dem Außendurchmesser anliegen. Das ist an beiden Enden nur bei einer geraden Zahl von Einzelfedern oder Federpaketen möglich.
Innerhalb einer Federsäule liegt immer eine etwas ungleichmäßige Einfederung der einzelnen Tellerfedern vor. Dies führt natürlich zu einer Überlastung der Federn an einem Ende der Federsäule und einer entsprechend verkürzten Lebensdauer. Dies ist auch der Grund dafür, dass bei dynamischer Belastung die ersten Brüche in den allermeisten Fällen an einem Ende der Federsäule auftreten. Wir empfehlen deshalb ein Ausrichten der leicht vorgespannten Federsäule. Dies kann z.B. in einem Prisma geschehen. Nach erfolgtem Ausrichten sollte die Federsäule nicht mehr völlig entspannt werden. Dieses Ausrichten hat sich in der Praxis zur Verminderung der Reibung sehr gut bewährt. Ist das Ausrichten aus konstruktiven Gründen nicht möglich, dann kann die Säule ein- oder mehrmals bis zur Flachlage zusammengedrückt werden. Auch dies bringt eine Reibungsverminderung, da sich die Federn dadurch etwas zentrieren.
nach oben
|
|
Welche Toleranzen gelten für Tellerfedern?
Die nachfolgend aufgeführten Grenzabweichungen sind in DIN EN 16983 festgelegt. Sie gelten für alle SCHNORR Tellerfedern nach DIN und Werksnorm. Auch für Sondergrößen wenden wir im Allgemeinen diese Toleranzen an, lediglich bei Federn, die in den Maßverhältnissen stark von den DIN-Federn abweichen, müssen größere Toleranzen festgelegt werden. Dies gilt z.B. für SCHNORR Kugellager-Tellerfedern K. Wenn engere Toleranzen gewünscht werden, als sie in DIN EN 16983 vorgeschrieben sind, bitten wir um Rücksprache.
|
|
|
Durchmessertoleranzen
Für den Außendurchmesser De gilt Toleranzfeld h12, für den Innendurchmesser Di Toleranzfeld H12. Für die Koaxialität gilt: für De bis 50 mm: 2 · IT 11 für De über 50 mm: 2 · IT 12
|
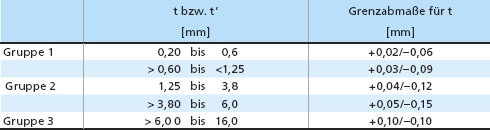
|
Dickentoleranzen
Nach DIN EN 16983 sind folgende Abweichungen zulässig: Bei Federn der Gruppe 3 gelten die Grenzabmaße für die reduzierte Dicke t’. SCHNORR benutzt die Dicke als Fertigungsausgleich und weicht deshalb in manchen Fällen von obigen Werten ab.
|
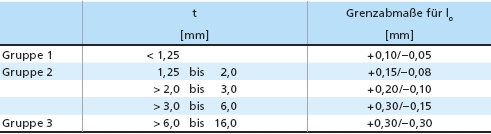
|
Höhentoleranzen
Zur Einhaltung der vorgeschriebenen Federkräfte lässt DIN EN 16983 eine geringfügige Überschreitung der Bauhöhentoleranz zu.
|
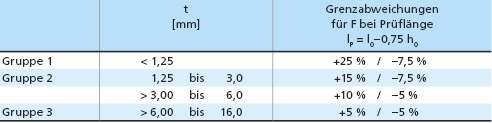
nach oben
|
Krafttoleranzen
Die Federkraft muss am Einzelteller bei der Prüflänge l0–s geprüft werden. Dabei muss die Feder unter Verwendung eines geeigneten Schmiermittels zwischen zwei gehärtete, geschliffene und polierte Platten gelegt werden. Es wird stets beim Belasten der Feder gemessen.
|
Wie gross ist das Spiel zwischen Tellerfedern und Führung auszulegen?
Tellerfedern erfordern immer ein Führungselement, um das seitliche Verrutschen unter Last zu verhindern. Die Führung kann sowohl am Innendurchmesser Di als auch am Außendurchmesser De erfolgen. Meist wird die Innenführung auf einem Bolzen oder einer Welle der Außenführung in einer Hülse vorgezogen, weil sie konstruktive und wirtschaftliche Vorteile bietet.
Für das Spiel zwischen Führungselement und Feder empfiehlt die DIN EN 16983 die Werte der nebenstehenden Tabelle.
Diese Werte stellen die Differenz der Durchmesser dar. Unter bestimmten Voraussetzungen kann das Führungsspiel verringert werden, z.B. bei Federn auf schnellaufenden Spindeln.
Die Führungselemente und die Auflagen sollen nach Möglichkeit einsatzgehärtet sein (Einhärtetiefe ca. 0,8 mm) und eine Mindesthärte von 55 HRC aufweisen. Die Oberfläche der Führungselemente soll glatt und möglichst geschliffen ein. Besonders bei dynamischer Belastung empfehlen wir eine Schmierung mit molybdändisulfidhaltigem Fett. Bei statischer Belastung können auch ungehärtete Führungsteile ausreichend sein.
nach oben
|
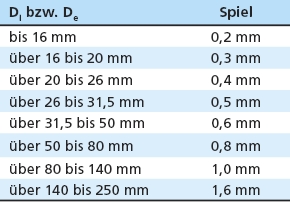
|
Welche Bedeutung haben Reibungseinflüsse bei Tellerfedern?
Durch die Reibung entstehen bei einer Tellerfedersäule stets mehr oder weniger große Abweichungen der tatsächlichen Be- und Entlastungskennlinie von der rechnerischen Kennlinie. Diese Abweichungen sind in vielen Fällen störend, sie können jedoch auch erwünscht sein. Es ist daher oft notwendig, die Reibung in Betracht zu ziehen und ihre Größenordnung abzuschätzen bzw. rechnerisch zu ermitteln.
Die Reibung bei Tellerfedern setzt sich aus 4 verschiedenen Komponenten zusammen:
1. Reibung an den Endanlagen durch die radiale Bewegung zwischen Tellerfeder und Anlagefläche. Sie tritt nur zwischen den letzten Federn einer Säule und den anliegenden Teilen auf. Die innerhalb einer Säule liegenden Federn führen die gleiche Radialbewegung aus, so dass keine Reibung entsteht. 2. Innere Reibung durch elastische Verformung des Werkstoffes. Sie entsteht bei jeder elastischen Verformung eines Stoffes und kann nicht beeinflusst werden. 3. Reibung an den Führungselementen durch Entlanggleiten der Tellerfedern während der Einfederung. 4. Reibung zwischen zwei Federn bei Parallelschichtung.
Die ersten drei Reibungsarten treten nicht nur bei einfach geschichteten Tellerfedersäulen, sondern auch bei einzelnen Tellerfedern auf. Aus diesem Grund ist bei Tellerfedern die Reibung meist etwas größer als z.B. bei Schraubenfedern.
Die Größe der Reibung hängt von sehr vielen Einflüssen ab:
Geometrische Faktoren:
- Form des Federquerschnitts
- Rundung der Kanten
- Größe des Führungsspiels
- Oberflächenrauhigkeit der Federn und Führungsteile
Werkstofftechnische Faktoren:
- Werkstoff der Federn und Führungteile
- Härte der Federn und Führungsteile
- Oberflächenbeschichtung der Federn
- Art des Schmiermittels
Konstruktionsbedingte Faktoren:
- Anzahl der parallel geschichteten Federn
- Länge der Federsäule
Belastungsabhängige Faktoren:
- Größe des Federhubes
- Geschwindigkeit der Belastung (Frequenz)
Der Anteil dieser einzelnen Faktoren an der Gesamtreibung ist natürlich sehr unterschiedlich und von Fall zu Fall erheblichen Schwankungen unterworfen. Bei der Vielzahl der Einflüsse ist eine genaue Berechnung der Reibung verständlicherweise nicht möglich. Aus vielen Versuchen mit den verschiedensten Federgrößen ergibt sich ein Richtwert für die Größe der Reibung von etwa ± 2,5% je Schichtung (+ Belastung, – Entlastung).
Die Reibungskräfte wirken entgegen der jeweiligen Bewegungsrichtung, d.h. bei Belastung der Feder müssen sie zusätzlich überwunden werden und erhöhen scheinbar die Federkraft, bei Entlastung wirken sie in umgekehrter Richtung und verringern die nach außen abgegebene Kraft. Zwischen tatsächlicher Be- und Entlastungskurve entsteht eine Hystereseschleife, deren Flächeninhalt im Kraft/Federweg-Diagramm die Reibungsarbeit darstellt. Diese Reibungsarbeit wird vollständig in Wärme umgesetzt und kann bei dynamischer Belastung mit hoher Frequenz zu einer ganz erheblichen Erwärmung führen. In solchen Fällen sind 1-fach geschichtete Federsäulen unbedingt vorzuziehen und auf gute Schmierung muss besonders geachtet werden.
Betrachtet man die Feder als Arbeitsspeicher, dann geht die Reibungsarbeit verloren; sie wird nicht wieder abgegeben. Bei Pufferfedern ist dieser Effekt erwünscht, bei Schwingungssystemen ist die Reibungsarbeit ein Maß für die Dämpfung.
nach oben
|
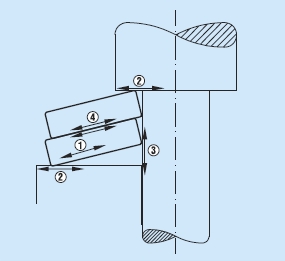
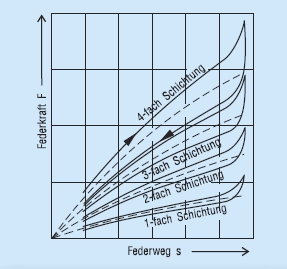
|
Weshalb werden Tellerfedern vorgesetzt?
Nach der Wärmebehandlung wird jede Feder mindestens einmal flachgedrückt. Dabei verringert sich die Bauhöhe, die Feder wird plastisch verformt. An der Oberseite entstehen Zugeigenspannungen, die den bei folgenden Belastungen auftretenden Lastspannungen entgegenwirken und somit Spannungsspitzen abbauen. Dadurch wird eine weitere plastische Verformung bei späteren Belastungen der Feder vermieden.
nach oben
|
|
|
|
|
|
|